Tailing Dam
Share this page
Exposed and covered liner integrity testing at Tailing Dam – Gold mining
A tailing dam is typically an earth-filled embankment dam used to store byproducts of mining operations after separating the ore from the gangue. Stored tailings can be liquid, solid or slurry of fine particles and are usually highly toxic.
Therefore protection of the environmental surroundings of the tailing dam should be the highest priority. To stop leaking toxic material from the tailing dam to its sub-grade which then contaminates the groundwater SENSOR DDS® technology should be used. To test the integrity of the sealing layer of a tailing dam after its installation to detect and locate the leaks we use our Arc Tester – SENSOR DDS® MIT. For testing geomembrane integrity after placing an overliner (gravel) we use Sensor’s dipole testing kit SENSOR DDS® Mobile.
Arc Tester – SENSOR DDS® MIT and SENSOR DDS® Mobile dipole survey
Example project info:
- Area tested was 283 000m²
- Single layer of HDPE 1.5mm geomembrane installed
- Protective layer: 500mm gravel
- For exposed liner testing Arc Tester SENSOR DDS® MIT was used
- For covered liner testing SENSOR DDS® Mobile was used
During the testing of bare geomembrane integrity at Tailing dam at a gold mine project we detected and located 132 holes in total. Most of them represented cuts or weak extrusion welding. However holes caused by cigarette burns were also very frequent damage. The average productivity at this project was 9 500 m² per day per operator. We have visited site multiple times following the progress of geomembrane installation.
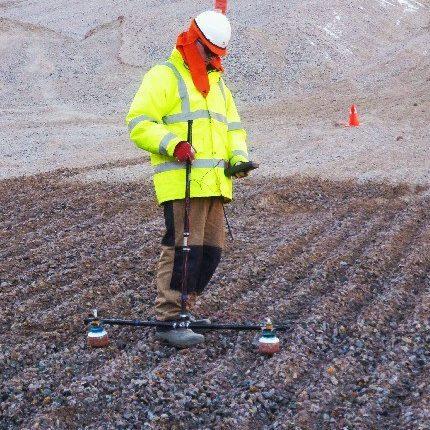
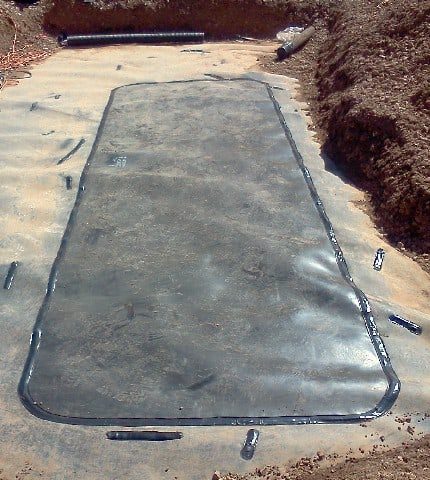
The installation of the overliner (drainage protective layer of gravel) took place after whole area of geomembrane was tested using Sensor DDS® technology. The total damage found during our testing was 102 holes. The most common damage (more then 50%) was caused by gravel penetrating through the liner from above. This happens when heavy machinery placed on the protective overlier presses onto the geomembrane forcing the gravel through the geomembrane. When the machinery turns sharply on the gravel it can also create large tears or cracks in the geomembrane.
We helped the client save a lot of time, issues and money by identifying these future leaks now. It’d be very expensive and technically difficult to repair these leaks when Tailing Dam would be in full operation.
Some photos from the SENSOR DDS® surveys at various Gold’s mine Tailing Dams
Help
Need more information about Sensor (UK), or our technologies and solutions? Talk to us today.