Sensor DDS® MIT
Waterless Geomembrane Arc Testing. ASTM D7953 Approved.
Share this page
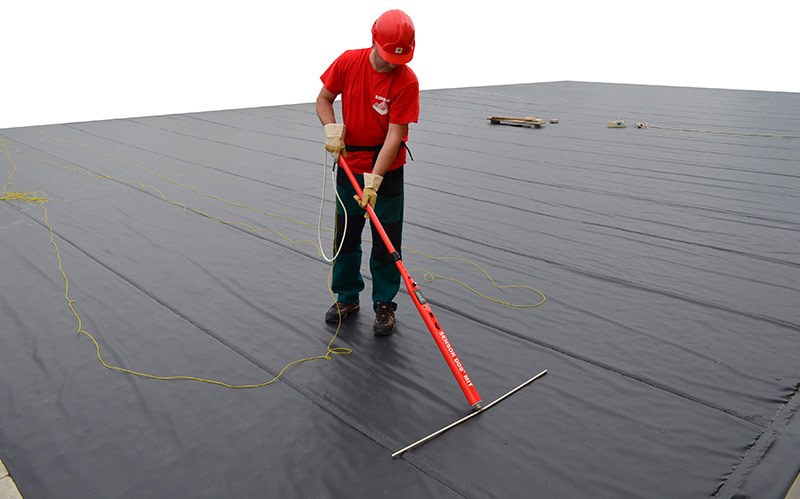
Sensor DDS® MIT technology was developed specifically for the testing and quality control of exposed geomembranes including synthetic waterproofing membranes, liners and asphalt systems.
It is applied to the exposed face of the liner directly after installation. The system electronically verifies the integrity of the entire surface including the welds enabling the elimination of all damage including pinholes.
When the damage is encountered the equipment will generate an audio-visual warning to the Technician making the equipment simple to use.
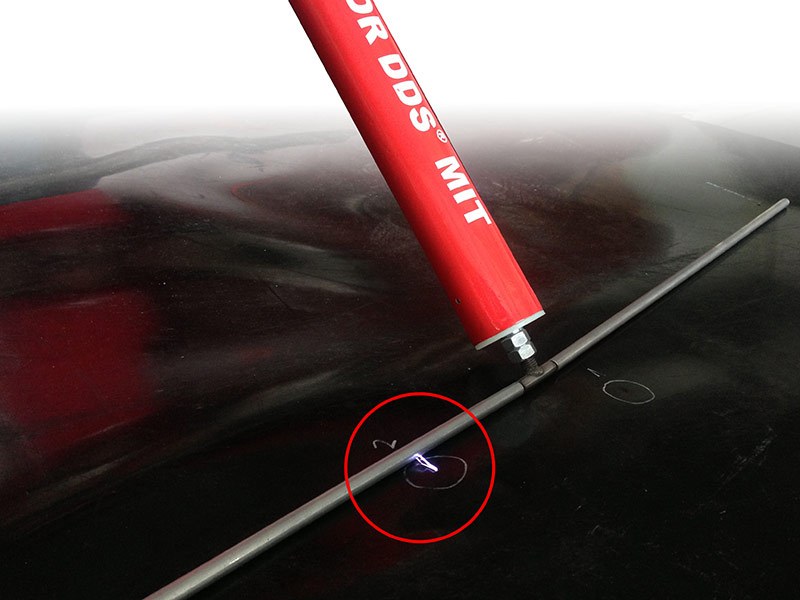
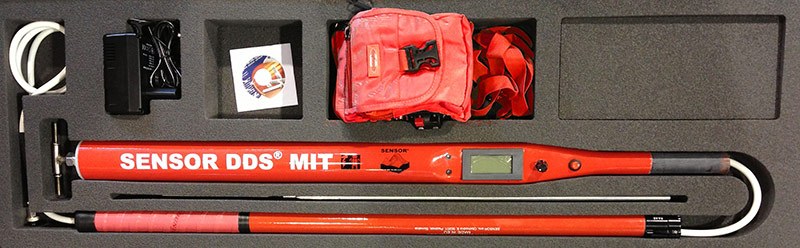
All geomembrane liner installations should be thoroughly tested to ensure complete integrity exists, prior to the placement of any covering media over the liner. Geomembranes put into service with existing damage will cause the early deterioration of the protection they can offer.
The standard quality control systems normally offered during liner installation concentrate solely on the welds and as such these controls will miss damage to the liner in mid-sheet areas.
Clients can be sure that the installer has provided a clean installation, whilst the installer is protected from claims for damage caused to the liner that occurs after the test date.
Advantages of Waterless Geomembrane Arc Testing:
- Cost effective
- No upfront cost
- Additional Quality Control for installation of geomembranes
- Electronic verification of integrity
- High voltage DC arc testing device
- Developed to further strengthen QC of geomembrane
- Generates an audio-visual alarm when damage is found
- Verifies the integrity of the entire surface (including welds)
- Identifies all damage caused by transit and installation
- Can detect even the smallest < 0.5mm pinhole damage
- Protection for the client and the installation contractor
- No water required to operate
- One operator can test up to 6000m² per day
- Zero interference between units
- Many operators can work simultaneously
- Minimal training is required
- Lightweight - the entire kit weighs only 2.5kg
Help
Need more information about Sensor (UK), or our technologies and solutions? Talk to us today.